From blown glass creations of days past to modern spacefaring contact lens experiments, we’ve come a long way. With smart lenses, microelectronics and drug delivery breakthroughs, the evolution of these little eye wonders presents a spectacular tale!
While Leonardo Da Vinci can be credited with initially conceptualizing the contact lens,1 it was German ophthalmologist Adolf Gaston Eugen Fick who successfully fabricated (and fitted) the first afocal scleral contact lens in 1888.2
Made from blown glass, they were large, cumbersome, and could only be worn for a few hours. However, technological and material advancements meant that by the late 1930s, lenses were being made entirely out of plastic, becoming essentially the early versions of the product we know today.
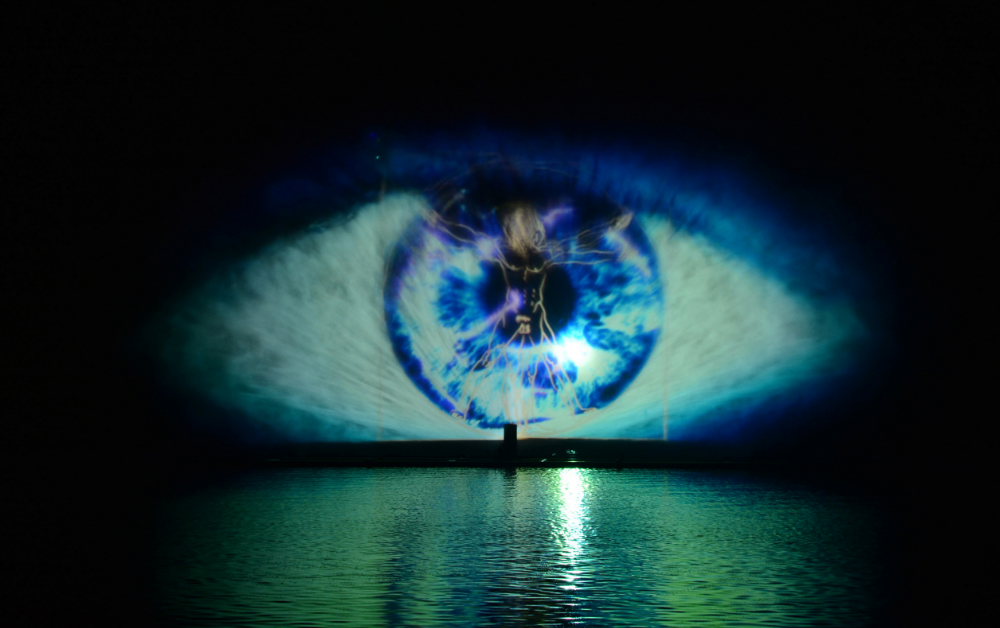
A patchy start
To fit and manufacture these rudimentary contact lenses, a mold was first created using an impression of the patient’s eyeball, and the lens was formed from this.
This was an uncomfortable process, as early scleral lenses often shifted out of alignment—or popped out altogether—as well as deprived the eye of oxygen.
Thankfully, the development and use of the keratometer eliminated the need for eyeball impressions. Reductions in lens diameter have also led to a more ergonomic product.
These days, lens manufacturers are constantly developing and advancing their products with different materials and technologies. However, the primary material used to produce contact lenses is still a plastic polymer—PMMA for hard lenses and PHEMA for soft contact lenses.
The modern-day process
There are two main ways in which modern-day contact lenses are manufactured: By cutting a blank on a lathe or injection molding.
Lathe cutting involves spinning the blank (also known as a ‘button’, a circular disk of lens material slightly larger than the desired finished product) on a digital lathe. Rotating at over 6000 rpm, a diamond or laser cutting tool shapes the curvature and thickness of the lens according to the patient’s specifications.
The lens is then buffed and polished to eliminate any imperfections, and a technician shapes the edge. Finished lenses are thoroughly tested and sterilized before packaging.
While the shaping process only takes around 15 minutes, an additional hydration stage (impregnating the lenses with liquid, making them soft and gel-like) can take another 24 hours. The whole procedure is computerized, ensuring quality and efficiency. This method of production can easily produce over 1,000 lenses per day.
Molding was originally done using the spin-casting technique. Three different liquids are poured into the mold and the centrifugal force of the spinning mold causes the polymerization of these fluids to form hydrophilic plastic. The outside curve of the lens is shaped by the mold, and the inside curvature is formed from the speed of rotation on the mold.
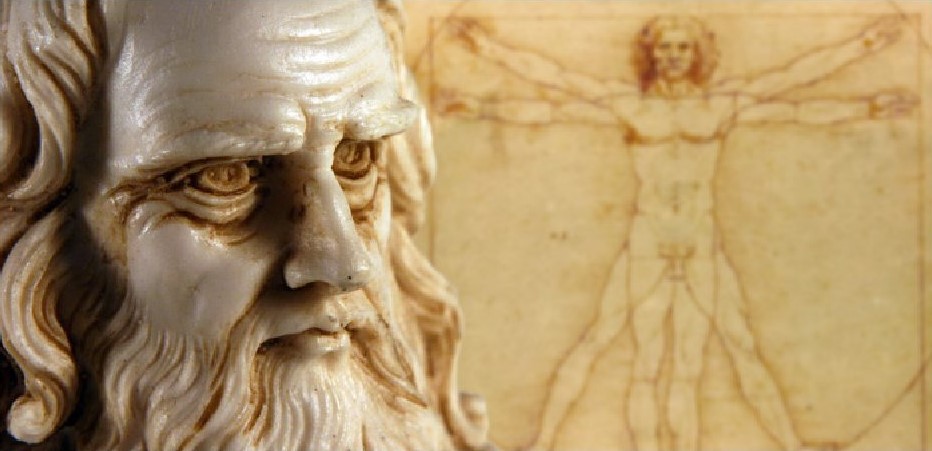
Injection molding involves injecting molten plastic into the mold under pressure. The lens is then removed from the mold and cooled before finishing on a lathe. Some modern computerized techniques allow for the lens to be finished entirely through the injection molding process.
From ortho-k to toric lenses, there’s a lens for everything these days. Bifocal, diffractive, monofocal, multifocal, and simultaneous vision lenses can also be fitted to treat presbyopia.3
The future looks clear
Continuous research and experimentation are underway to explore different materials and polymers. Siloxane, which allows 25 times more oxygen permeability compared to current standard lenses, promises game-changing implications—particularly for extended-wear contacts and scleral lenses.
There are even experiments with materials in outer space! Trials aboard the space shuttle Endeavour suggest the zero-gravity environment could lead to more oxygen-permeable and debris-resistant contact lenses.4
Triggerfish from Sensimed (Etagnières, Switzerland) is another example of the continuous technological innovation occurring within the contact lens space. Triggerfish is a soft lens made from hydrophilic hydrogel fitted with onboard microelectronics, which can monitor patient intraocular pressure (IOP) in real time. The lens can be worn for 24 hours, and recorded information is transmitted to a computer via Bluetooth.
With particular implications for glaucoma management, this device can help measure the effects of various factors such as medication, sleep patterns, and body position on IOP.5
Ocular drug delivery is another area in which contact lens innovation is showing promise. MediPrint Ophthalmics (California, USA) has developed a noninvasive drug delivery system using contact lenses. While still in its early phase, the system could have positive implications for the management of myopia, dry eye, allergy, and glaucoma, as well as post-cataract surgery treatments.6
So, from Da Vinci’s visionary experiments to zero-gravity manufacturing processes, along with sci-fi-inspired ocular drug delivery systems, the evolution of the trusty contact lens looks anything but blurry!
References
- Heitz RF, Enoch JM. Leonardo da Vinci: An assessment on his discourses on image formation in the eye. Advances in Diagnostic Visual Optics. 19-26, Springer-Verlag.
- Adolf Eugen Fick (1852-1937). Available at http://www.sciencemuseum.org.uk/broughttolife/people/adolfeugenfick.aspx. Accessed on August 3, 2023.
- Gurnani B, Kaur K. Contact Lenses for Presbyopia. Stat Pearls [Internet]. 2023 May 4.
- Contact Lenses. Available at http://www.madehow.com/Volume-2/Contact-Lens.html. Accessed on August 3, 2023.
- Dunbar GE, Shen BY, Aref AA. The Sensimed Triggerfish contact lens sensor: efficacy, safety, and patient perspectives. Clin Ophthalmol. 2017;11:875-882
- MediPrint’s drug-releasing contact lens reduces intraocular pressure in glaucoma patients. Available at https://www.medicaldevicenetwork.com/news/mediprints-drug-releasingcontact-lens-reduces-intraocular-pressure-inglaucoma-patients/. Accessed on August 3, 2023.
Editor’s Note: This article was published in COOKIE magazine Issue 13.